Jag Sandhu, Director at Tokyo Fabrics, talks about the importance of its continued use of Halogen FR treatments and why quality and safety should never be compromised.
Earlier this year at the January Furniture Show 2025, furnishing fabrics supplier Tokyo Fabrics displayed an array of new products, designs and innovations. Alongside this, an ‘Urgent Notice’ was also a key highlight, emphasising the company’s strong belief in the importance of Halogen Fire Retardant treatments.
Despite the rise in Halogen FR costs, which have risen to their highest in 30 years, Tokyo Fabrics maintains its commitment to using Halogen FR. Understanding the implications and potential consequences, the company is led by the science and fact-based results, hence the use of Halogen FR as opposed to halogen-free FR alternatives. “We will not gamble on safety, gathering and collating market intelligence, coupled with our four-decade experience, we know that halogen-based application is the clear leader when it comes to FR performance, outperforming halogen-free in numerous clinical tests,” Jag said.
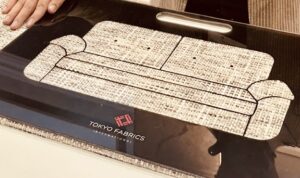
“There are fundamental problems surrounding Halogen-free FR options in the marketplace, which weigh heavily on our minds from a moral and ethical perspective. Until these issues are thoroughly investigated, addressed and resolved, we refuse to compromise our end users,” Jag continued. “For me, when you talk about a quality issue it can be subjective of course, in how people quantify different levels of quality standards and practices, however, from a compliance and safety standpoint, there’s no compromise whatsoever.
“The response has been very encouraging, we continue to engage and educate our customers about the differences in detail, which backed by intelligence and hard facts demonstrates our fierce pursuit of achieving absolute fire-retardant compliance.”
Not being under any illusion regarding the cost, Jag said that the core ethos of the business is to deliver excellence without compromise and maintain its strong core legacy, which it has built over the last 40 years, evident by the fact that if Tokyo Fabrics were to switch to a halogen-free FR formula, the company would make a saving of £60,000 per week – an annual saving of £3million.
“For us, whilst our profits may be getting impacted, our quality is not compromised,” Jag said. “Despite shouldering significant rising costs of Halogen FR, we believe it’s a sacrifice necessary for the peace of mind that underpins our robust track record. Our loyalty to our customers is paramount, demonstrating our commitment to their trust and satisfaction.
“Halogen-free is a lot more lucrative from a pricing perspective,” adds Jag, “it’s a lot more feasible and easily accessible, however what we’re finding is that the end customers product is compromised, unbeknown to them. All they feel is an applicant to the back of the fabric, so naturally they believe there’s a robust fire retardant guaranteeing the best FR performance, but the reality is halogen-free is increasingly being applied due to cost saving.”
Continued evolution of safety is crucial, as is the increase in industry-wide awareness. “With halogen-free, it’s not that it doesn’t comply with FR regulation, and we acknowledge it does, but the debate is the level of compliance,” Jag said. “Halogen is like a first degree at university, whereas halogen-free is like a 2:2 – still a pass but not at a greater level. It’s about educating the customer to know the difference between passes and make them interested to want to explore further. So, are we moving backwards in safety, or are we moving forward in terms of performance?”
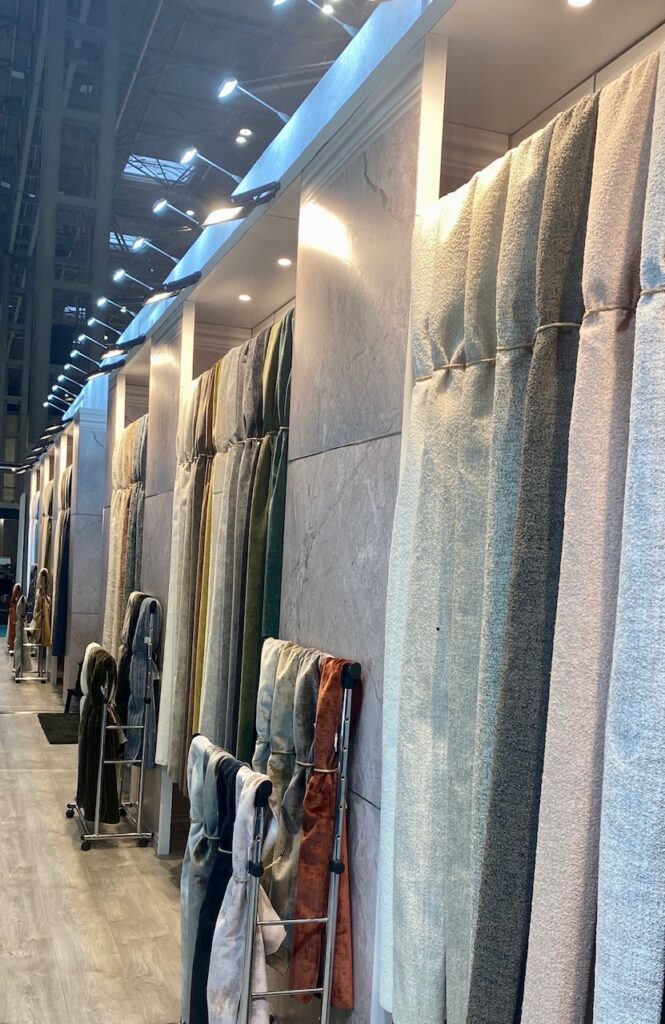
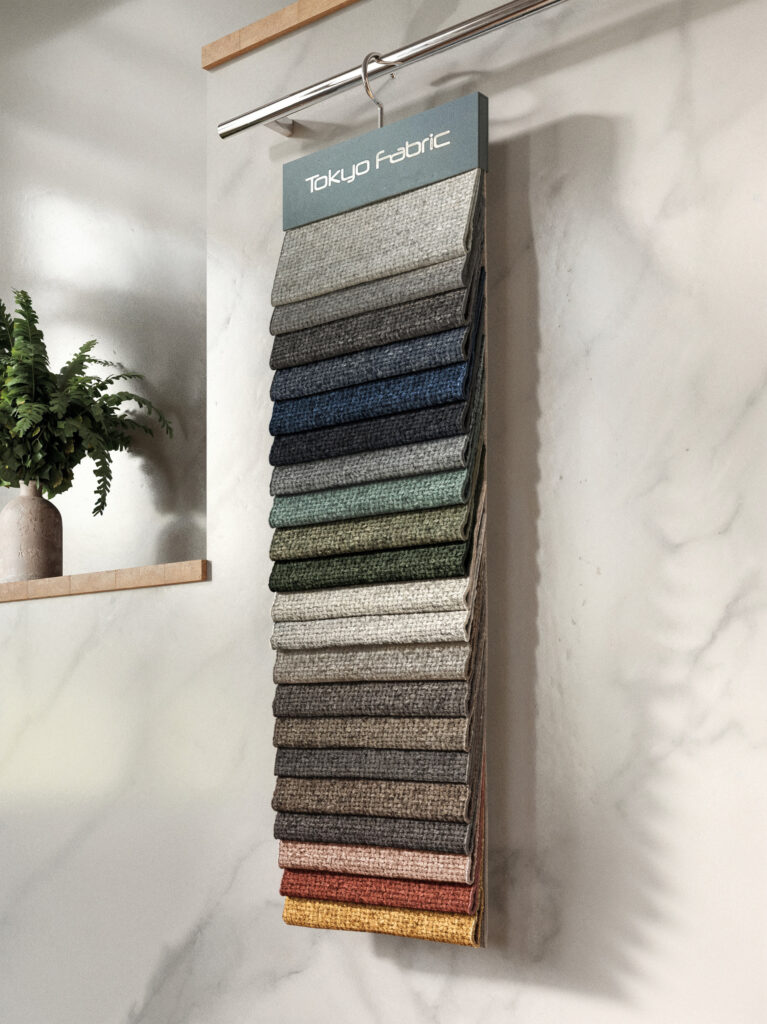
Jag also explained: “The second key point is the issue relating to halogen-free FR, which is the foul odour. I’ve seen numerous complaints from consumers on websites about those garlic or cheese odours from products. The red phosphorous used in the halogen free as a fire retardant in its original form has an unpleasant odour, so a neutralising chemical is further compounded in order to mask the original foul odour. This however, has notably caused issues under particular circumstances, whereby certain warm spaces and/or damp surroundings react to it and cause an even concentrated foul smell – which is what many consumers have experienced.”
Jag raises an interesting question and is aiming to continue the education journey within the industry, hoping to potentially raise the bar entirely in the use of FR treatments as standard. One area Tokyo Fabrics is already evolving is through testing. Jag said: “Whilst the British regulation requires two 20 second flame test, we do two 20 second flame tests followed by one 25 second and another 30 second test, showing we go above and beyond on our FR journey. The extra testing adds an extra string to our bow.”
Adding to Tokyo’s ongoing progression is the continuous investment across the business. The company has invested several million pounds into retardant machinery and is extending its factory footprint with a third site, expanding its capacity by another 100,000sqft – investing around £8-10million, which is all self-funded. “All our investment is organic, and it’s something to be proud of as we have paid up front in full for all our assets,” Jag said. “We’ve also invested in a new showroom, which is set to be unveiled this year. We’re excited to keep growing and one of the biggest statements I can make is that we currently carry 30 million plus meters in unsold stock. Our stock has a value of more than £100million and I’m confident in saying I don’t think there is anyone in our industry holding as much as we do.”
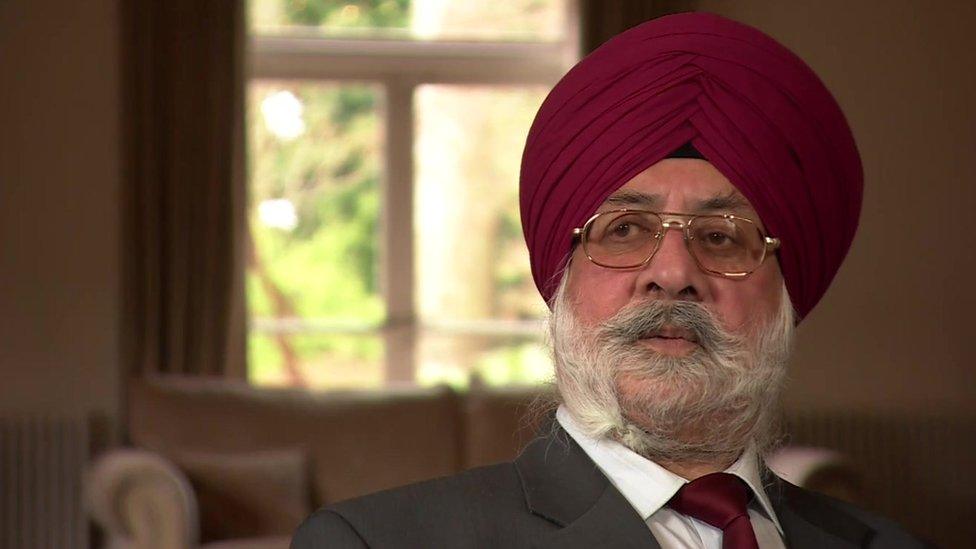
In terms of new products and designs, Jag kept this area close to his chest but was quick to pay testament to his family on the constant growth and success of the business, as well as its loyal customers. “We’re so very lucky to have my father in the business, who is 80 years young. He’s been, and continues to be, a big inspiration for our family and entire organisation – he is actually highly respected in all communities too.” Jag’s father Tarsem Singh Sandhu spearheaded a movement that saw Sikhs working on Wolverhampton’s buses win the right to wear a turban at work over 50 years ago. This has been documented and archived by BBC News and other media outlets. His story has also been published in a book ‘Transport & Turbans’.
Prior to this, Sikhs would shave and cut their hair in order to work on Wolverhampton’s buses. However, refusing to remove his turban or shave his beard, Tarsem Singh Sandhu campaigned against the uniform rules and sparked a dispute that went on to change legislation about religious expression at work. “I’m grateful to my father whose legacy and principles underpin the ethos of Tokyo Fabrics, shaping the company into what it is today,” Jag said.
Concluding on a final note on the topic of FR, Jag added: “We firmly believe that prioritising safety and quality is not just the right thing to do, but it is also a testament to our dedication to the customers we supply – we thank you for your understanding and continued support.”